voestalpine relies on FME technology for the digital twin
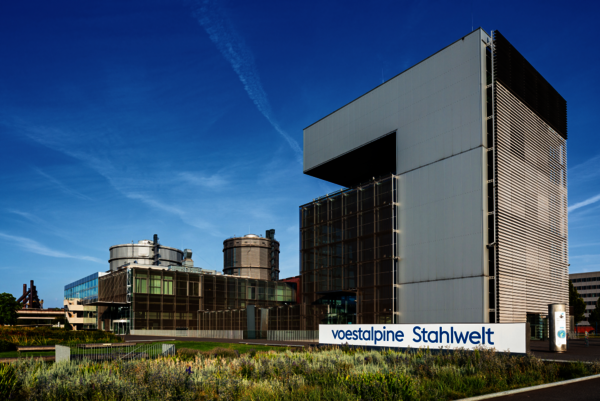
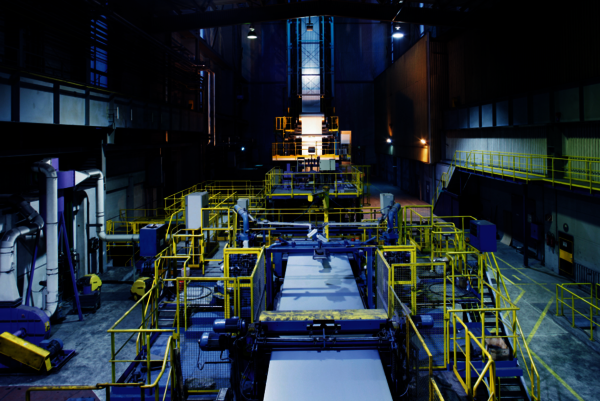
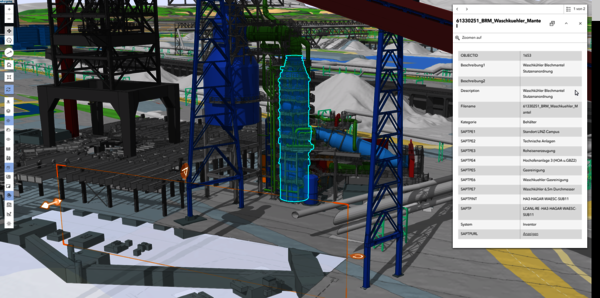
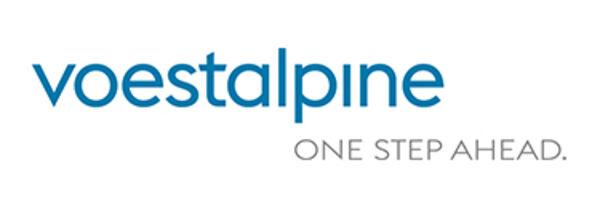
From data conglomerate to digital 3D campus: How voestalpine AG in Linz is bringing the digital twin to life with the help of FME.
voestalpine operates one of the most modern steel production sites in Europe at its industrial location in Linz. However, the vision of a complete digital twin of the entire campus presented the company with complex challenges. Numerous 3D models from different trades such as mechanical engineering, plant construction, solid construction and industrial building services were available in various formats and levels of detail. These heterogeneous databases were to be integrated into a standardized geographic information system (GIS) in order to create a comprehensive digital twin.
The particular challenge lay in the fact that suitable processes first had to be developed to prepare the existing models for further processing while retaining as much valuable information as possible. The conversion of CAD models from different systems required a powerful and flexible solution.
FME as the key technology for data integration
After intensive evaluation, IFC (Industry Foundation Classes) emerged as the most suitable data exchange format. The challenge, however, was the intelligent processing of this data. This is where the FME platform came into play, which made it possible to connect different transformers with each other in such a way that unnecessary model components were not transferred, but a visually appealing and information-rich result could still be transferred to the GIS.
As the transfer via IFC was still relatively new in 2016, the implementation was carried out in close cooperation with the experts from Safe Software, the developers of FME. This direct support was crucial to the success of the project and helped to overcome specific challenges during data conversion.
A growing 3D model with added value
Today, voestalpine has a continuously growing, detailed 3D model of the Linz industrial campus. This is far more than just a geometric representation of reality - it contains a wealth of information that offers analytical added value. As a result, queries and analyses can also be carried out in the third dimension in a similar way to the 2D map, which opens up completely new application possibilities.
Following the development of a stable FME workflow, adaptation for new systems is now possible quickly and easily. Although the concrete savings cannot yet be clearly quantified, voestalpine emphasizes the enormous benefits of the consistent 3D model.
Further development and automation
voestalpine is already working on further improvements to the system. One focus is on increased automation capability. Currently, the positions of the models (xyz and rotation) are still “hard-coded” in FME. Concepts are being developed to transfer this information directly in the exchange formats, which will further simplify the process.
Another innovative approach is to enrich the 2D CAD data with essential information in order to lift it into the third dimension and thus open up new basic data for the digital twin. This demonstrates the continuous effort to further develop the digital twin and maximize its benefits.
Success with axmann and FME
Are you facing similar challenges when integrating different 3D data sources? The voestalpine success story shows that with the right technology and the right partner, even complex data transformations can succeed.